
From the courtroom to the stage: How a St. Paul’s summer program brings students from 61 New Hampshire schools together
Earlier this month, New Hampshire federal judge Joseph Laplante passed along a last-minute message to administrators of a high school program at Concord’s St. Paul’s School: His courtroom was about to become the national epicenter of the fallout from President Trump’s executive order on birthright citizenship, and Laplante, an alumnus of the program, thought this year’s students ought to be there.

Officials identify victim in fatal Concord fire that displaced 12 residents
Charred remnants of vinyl cladding still hang from the second-story windows of a Concord apartment building, the aftermath of last week’s destructive fire that tore through the 10-unit complex at 151 Manchester St.
Most Read
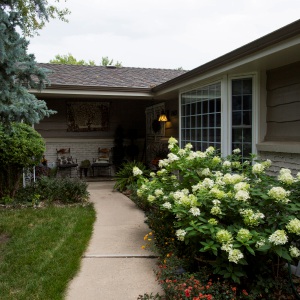





Editors Picks




Sports

Bow Brook Tennis Club hosts men’s A and B tournaments
The Bow Brook Club has a long history in Concord. Every year, except during breaks during both world wars, it has hosted a citywide men’s tennis tournament on red clay.




Opinion

Opinion: Trumpism in a dying democracy





Your Daily Puzzles
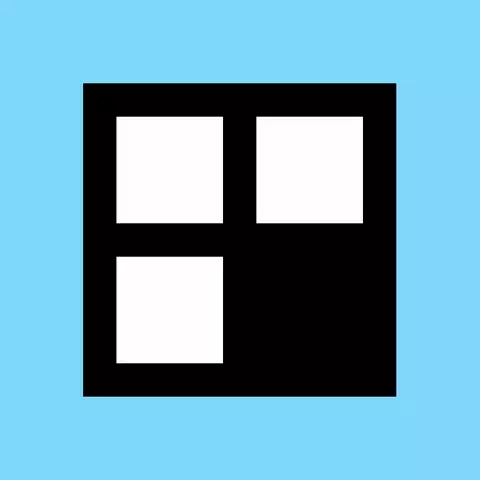
An approachable redesign to a classic. Explore our "hints."
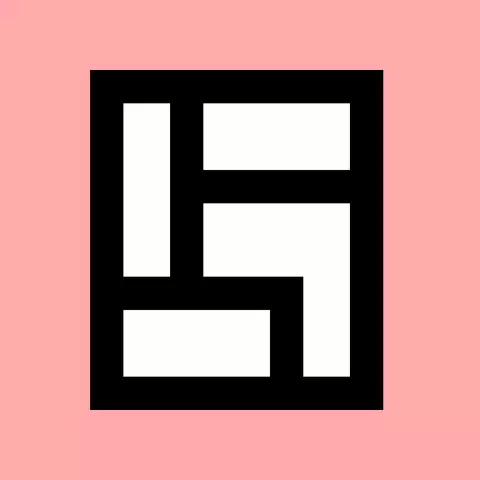
A quick daily flip. Finally, someone cracked the code on digital jigsaw puzzles.
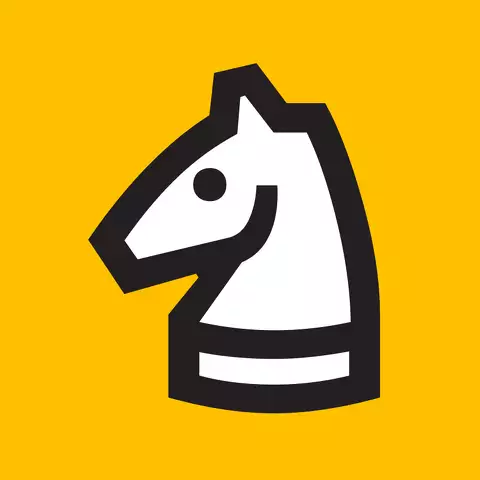
Chess but with chaos: Every day is a unique, wacky board.
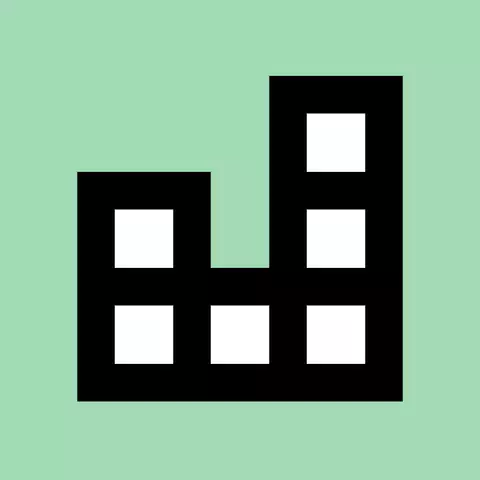
Word search but as a strategy game. Clearing the board feels really good.
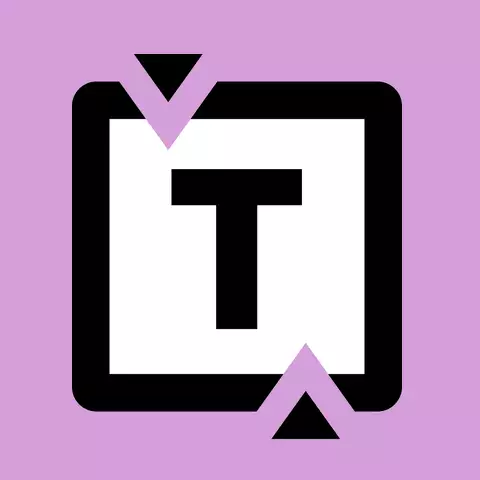
Align the letters in just the right way to spell a word. And then more words.
Politics

New Hampshire school phone ban could be among strictest in the country
When Gov. Kelly Ayotte called on the state legislature to pass a school phone ban in January, the pivotal question wasn’t whether the widely popular policy would pass but how far it would go.
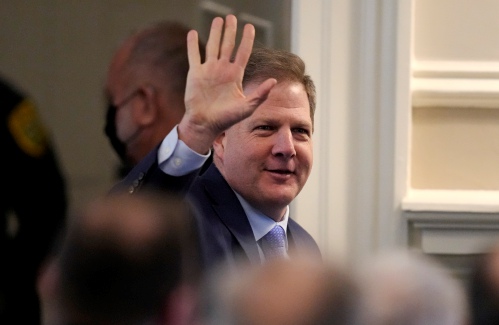
Arts & Life

Community Players of Concord celebrate 97th season, prepare for 98th
To celebrate the conclusion of their 97th season, the Community Players of Concord came together for an annual meeting including a pot-luck dinner and the presentation of a number of theatrical awards.


Obituaries
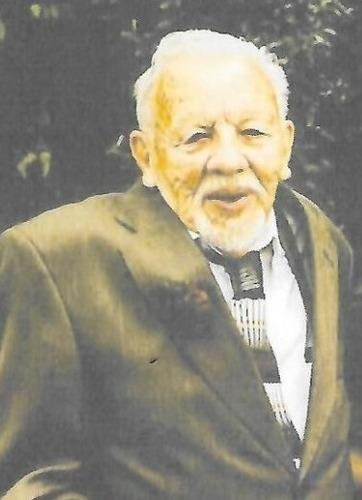
Hillsboro, NH - David F. Whitney 87, a lifelong resident of Hillsboro, NH., joined his bride Patricia A. (Wing) Whitney in Heaven Thursday June 26,2025. Born September 10, 1937 to Harry L. and Harriett S. Whitney at their home on Wh... remainder of obit for David Franklin Whitney
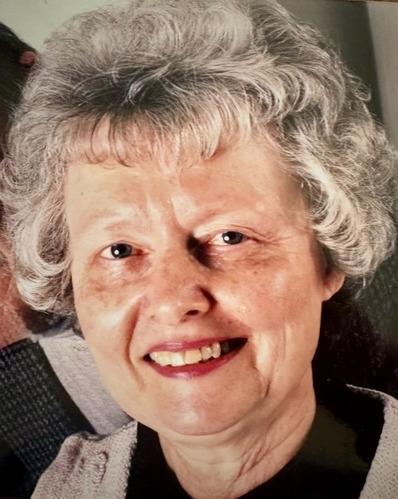
Concord, NH - Myrna Braley Prevost, 88, died on July 11 at The Birches in Concord, New Hampshire. She was predeceased by her beloved husband of 62 years, Fernand Prevost. Myrna was born August 20, 1936, in Franklin, New Hampshire. The ... remainder of obit for Myrna Prevost
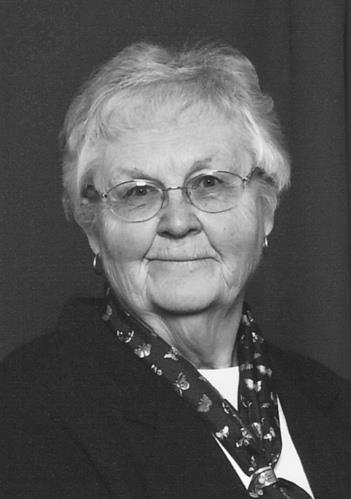
Concord , NH - ANNETTE LAMOREAU WOLFE Passed away surrounded by family on -5/9/2025 at the age of 88 yrs old. She was born in Presque Isle, Maine, the daughter of the late Paul Lamoreau and Ruth (Hasey) Lamoreau. Annette is survived by ... remainder of obit for Annette Lamoreau Wolfe
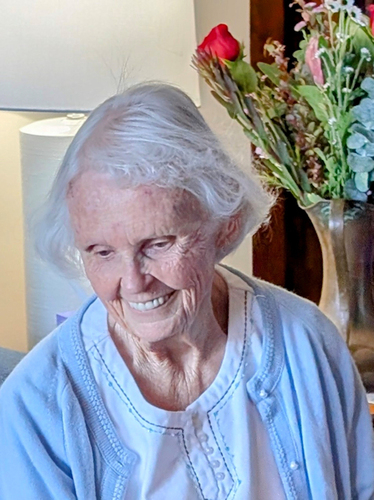
Tilton, NH - Dorothy Jacqueline "Jackie" Lavigne, a native of Nashua NH and a longtime prior resident of Tilton, NH and of Prescott Valley, AZ passed away on July 3, 2025 at the age of 92, with her devoted children by her bedside. A... remainder of obit for D. Jacqueline Lavigne