
New Cheers owners honor restaurant’s original menu while building something fresh
Greg Tandy started asking around when he became the new owner of Cheers.

‘Love you more’: Concord community remembers Glenn Chrzan
Deborah Eckland stood in front of section 47 at the New Hampshire State Veterans Cemetery, facing a small crowd of about a dozen people. She wiped her eyes with a white handkerchief.
Most Read






Editors Picks




Sports

Youngsters Richardson and Hakala move on, and veterans crash out at 122nd State Amateur Championship
ROCHESTER — Every golfer has A routine. Superstitions, lucky charms and a specific way of finding a mental sweet spot aren’t specific to the sport.


Opinion

Opinion: Trumpism in a dying democracy





Your Daily Puzzles
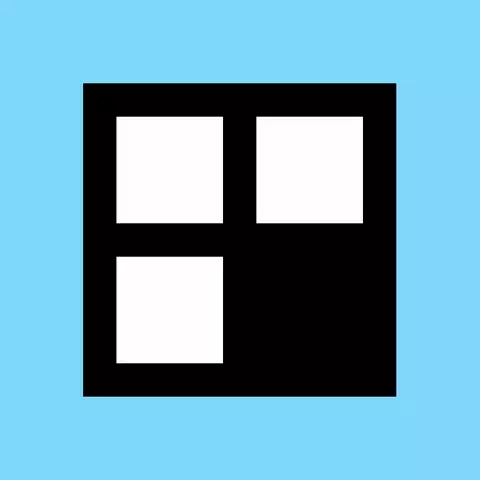
An approachable redesign to a classic. Explore our "hints."
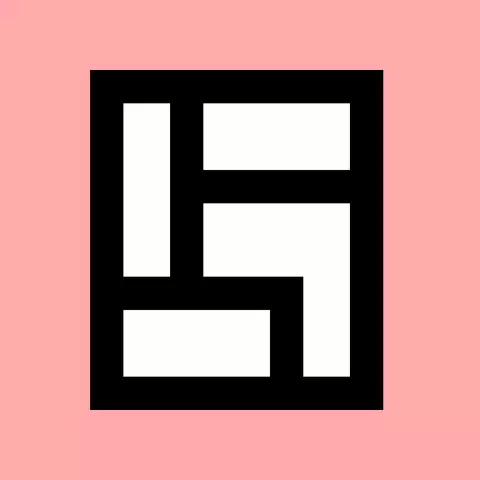
A quick daily flip. Finally, someone cracked the code on digital jigsaw puzzles.
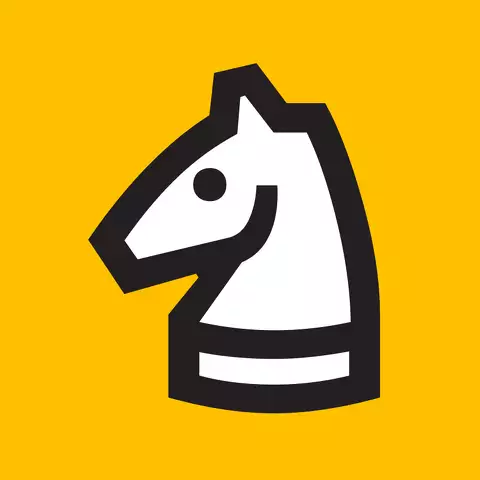
Chess but with chaos: Every day is a unique, wacky board.
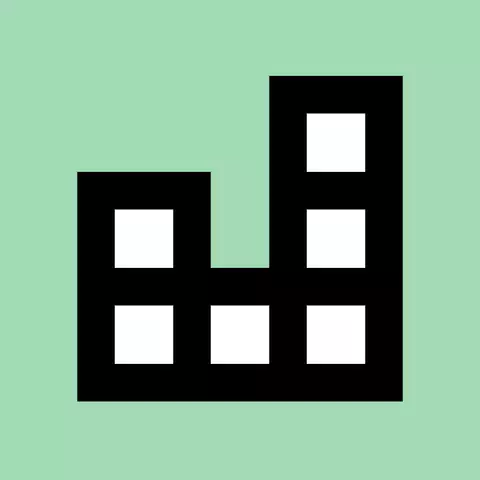
Word search but as a strategy game. Clearing the board feels really good.
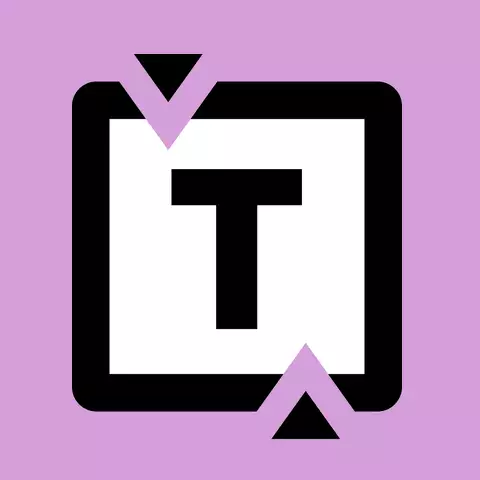
Align the letters in just the right way to spell a word. And then more words.
Politics

New Hampshire school phone ban could be among strictest in the country
When Gov. Kelly Ayotte called on the state legislature to pass a school phone ban in January, the pivotal question wasn’t whether the widely popular policy would pass but how far it would go.
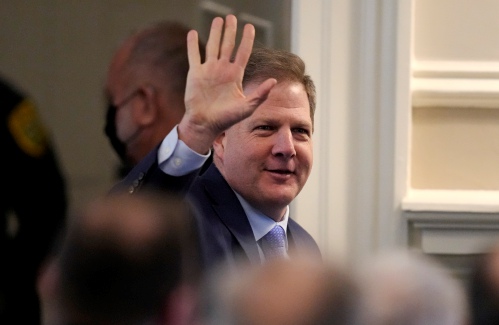
Arts & Life

Lavender haze: Purple fields bloom at Warner farm
The lavender fields at Pumpkin Blossom Farm in Warner are open for Harvest Days.




Obituaries
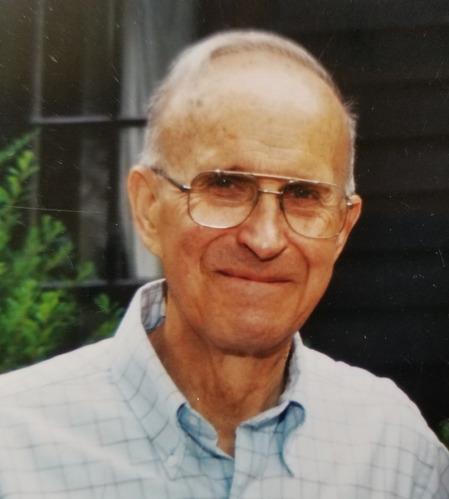
Concord, NH - Herbert E. "Herb" Little died on the evening of July 6, 2025, at Havenwood Heritage Heights in the room he shared with his loving wife Debby who was, as always, by his side. He was 97 years old having been born on Septembe... remainder of obit for Herbert Little
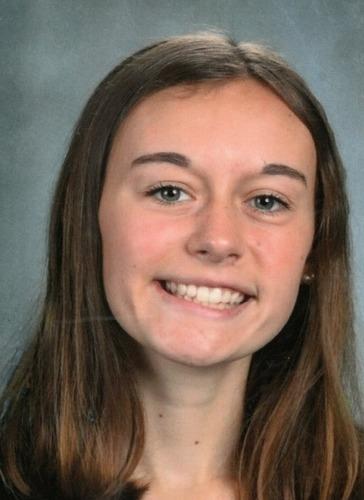
Contoocook, NH - Anna Marie O'Reilly, 21, of Contoocook, passed away unexpectedly at home on Friday, July 4, 2025. She was born on June 10, 2004, in Concord, NH to her parents, Joseph P. O'Reilly and Donna M. (Phillips) O'Reilly. Anna g... remainder of obit for Anna Marie O'Reilly
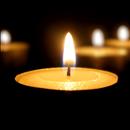
Baltimore, MD - Mary Ann Hermann died in her home in Baltimore on July 5, 2025, following a battle with cancer. She was 91. Mary Ann was a retired psychiatric nurse who worked in hospitals and visiting patients at their homes in Cuba, ... remainder of obit for Mary Ann Hermman
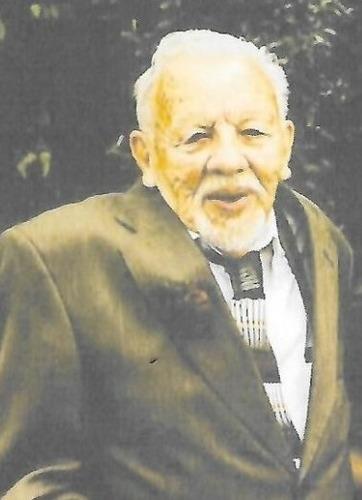
Hillsboro, NH - David F. Whitney 87, a lifelong resident of Hillsboro, NH., joined his bride Patricia A. (Wing) Whitney in Heaven Thursday June 26,2025. Born September 10, 1937 to Harry L. and Harriett S. Whitney at their home on Wh... remainder of obit for David Franklin Whitney