
‘A little piece of everything I like’: New Pittsfield barbershop brings more than a haircut to downtown
With a 1940s barber pole marking the outside and the fresh smell of a clean shave wafting from the window, the new single-chair barbershop is impossible to miss from downtown Pittsfield.

New Hampshire targets sexual exploitation and human trafficking inside massage parlors
Dark curtains drawn tight, doors locked at all hours, surveillance cameras inside the building and unusual business hours — these are all warning signs that a massage parlor may be a front for something more than therapeutic services.
Most Read






Editors Picks




Sports

Athlete of the Week: Grace Saysaw, Concord High School
Concord High junior Grace Saysaw cemented herself as one of the Crimson Tide’s best sprinters of the past few years with a record-breaking end to the spring.

Opinion

Opinion: Trumpism in a dying democracy





Your Daily Puzzles
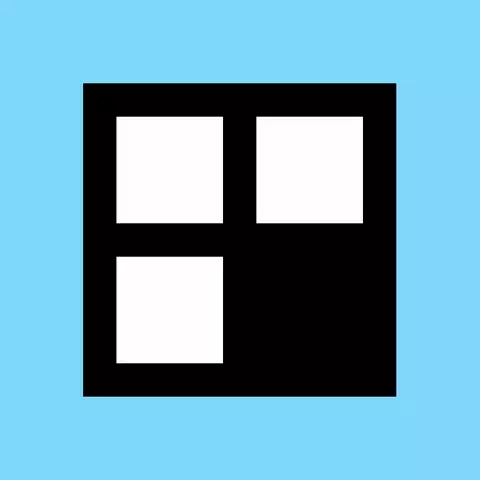
An approachable redesign to a classic. Explore our "hints."
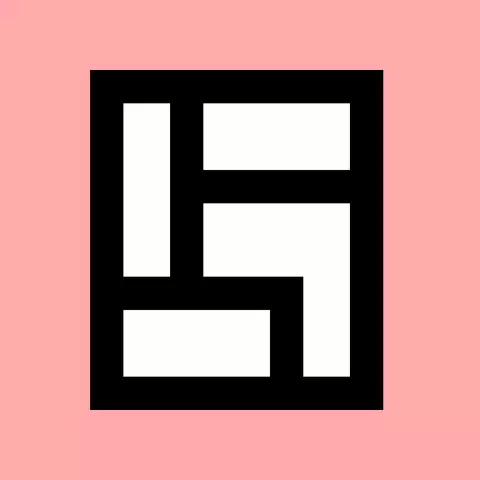
A quick daily flip. Finally, someone cracked the code on digital jigsaw puzzles.
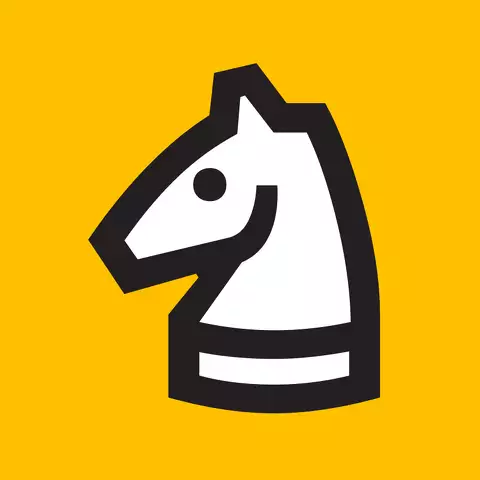
Chess but with chaos: Every day is a unique, wacky board.
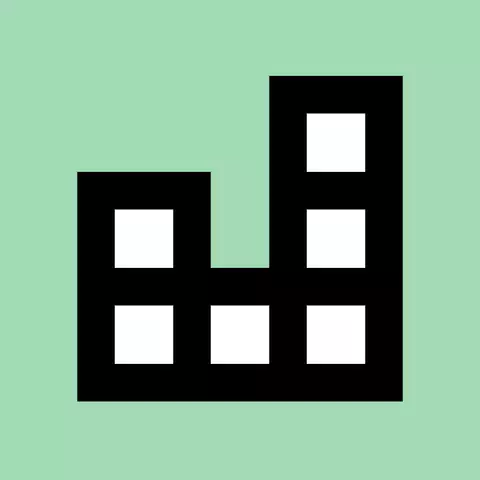
Word search but as a strategy game. Clearing the board feels really good.
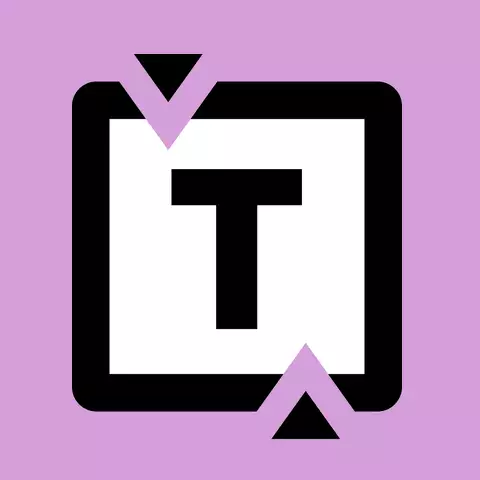
Align the letters in just the right way to spell a word. And then more words.
Politics

New Hampshire school phone ban could be among strictest in the country
When Gov. Kelly Ayotte called on the state legislature to pass a school phone ban in January, the pivotal question wasn’t whether the widely popular policy would pass but how far it would go.
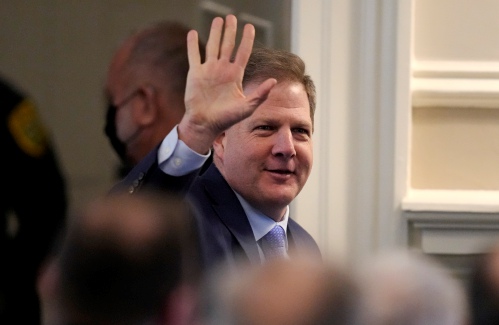
Arts & Life

Lavender haze: Purple fields bloom at Warner farm
The lavender fields at Pumpkin Blossom Farm in Warner are open for Harvest Days.




Obituaries
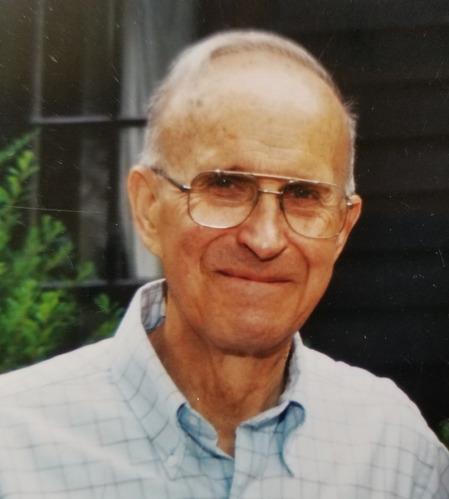
Concord, NH - Herbert E. "Herb" Little died on the evening of July 6, 2025, at Havenwood Heritage Heights in the room he shared with his loving wife Debby who was, as always, by his side. He was 97 years old having been born on Septembe... remainder of obit for Herbert Little
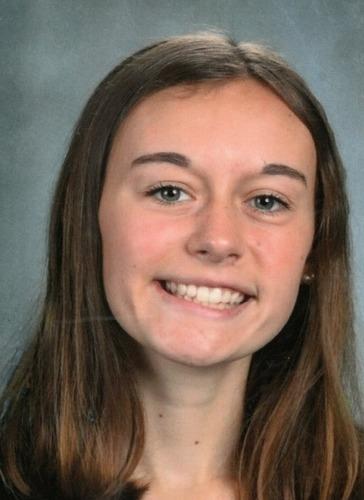
Contoocook, NH - Anna Marie O'Reilly, 21, of Contoocook, passed away unexpectedly at home on Friday, July 4, 2025. She was born on June 10, 2004, in Concord, NH to her parents, Joseph P. O'Reilly and Donna M. (Phillips) O'Reilly. Anna g... remainder of obit for Anna Marie O'Reilly
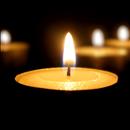
Baltimore, MD - Mary Ann Hermann died in her home in Baltimore on July 5, 2025, following a battle with cancer. She was 91. Mary Ann was a retired psychiatric nurse who worked in hospitals and visiting patients at their homes in Cuba, ... remainder of obit for Mary Ann Hermman
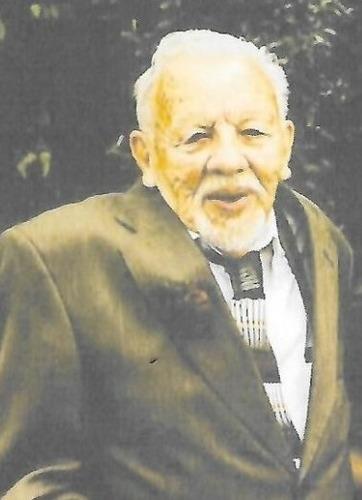
Hillsboro, NH - David F. Whitney 87, a lifelong resident of Hillsboro, NH., joined his bride Patricia A. (Wing) Whitney in Heaven Thursday June 26,2025. Born September 10, 1937 to Harry L. and Harriett S. Whitney at their home on Wh... remainder of obit for David Franklin Whitney